At TEC Aerospace, our in-house manufacturing capabilities are central to our ability to deliver mission-critical military parts with uncompromising precision and reliability. We strategically utilize a fleet of advanced, American-made Haas CNC machines to handle a wide range of production demands. Our Haas Milling machines, including versatile VF-Series and 5-axis machining centers, allow us to produce components with complex geometries, such as hydraulic manifolds and structural airframe parts, from advanced materials like titanium and high-strength alloys. For rotational components, our Haas ST-series CNC lathes are indispensable. Equipped with live tooling and Y-axis capabilities, these machines enable us to perform multiple operations like turning, milling, and drilling in a single setup, ensuring exceptional accuracy and concentricity for parts like MIL-SPEC fasteners, sleeves, and spacers. Complementing these are our high-speed Haas Drill & Tap centers, which leverage high-RPM spindles and rapid rigid tapping to efficiently produce the precise, numerous threaded features common in military assemblies. This integrated ecosystem of Haas machinery forms the backbone of our commitment to producing high-quality components that meet the stringent tolerances and performance standards required by the defense industry.
CNC Department
HAAS ST-10
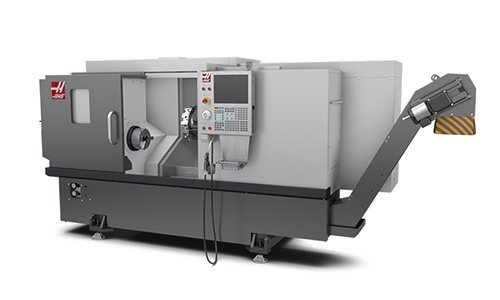
The HAAS ST-10 is a compact, high-performance CNC turning center designed for precision and efficiency in small-part machining. It features a small footprint while offering a robust build, high spindle speeds, and excellent thermal stability. Key characteristics include:
- Maximum cutting diameter: ~12.0" (305 mm)
- Maximum cutting length: ~14.0" (356 mm)
- Spindle speed: up to 6,000 RPM
- Spindle power: 15 hp (11.2 kW)
- Turret: 12-station bolt-on or optional live tooling
- Controller: Haas Next Generation Control (NGC)
HAAS ST‑20
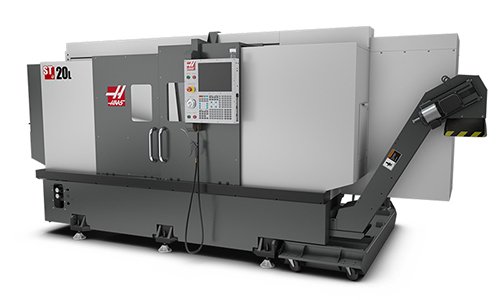
The HAAS ST‑20 is a rugged, mid‑size CNC turning center designed for high-volume, precision machining with small to medium parts. It offers a:
- 13″ (330 mm) maximum cutting diameter and 22.5″ (572 mm) Z-axis travel
- 2.5″ (63.5 mm) spindle bore, supporting bar-fed operations
- 20 hp (14.9 kW) belt-driven spindle at up to 4,000 rpm, mated to an A2–6 nose
- 12-station bolt-on or VDI turret, fast rapids (~945 ipm), and excellent chip evacuation
- Compact yet rigid design—11% smaller footprint than previous model—with built-in Wi‑Fi and optional automation like auto-door, parts catcher, sub-spindle, or APL
HAAS SL‑10

The HAAS SL‑10 is a compact, reliable two-axis CNC lathe tailored for small to medium-sized precision turning jobs. Here's a concise overview:
- Turning capacity: Up to ~11″ (279 mm) diameter and ~14″ (356 mm) length between centers haascnc.com+11machinestation.us+11cncmachines.com+11
- Spindle: Belt-driven A2‑5 nose, 15 hp (11.2 kW), 6,000 rpm top speed machinetools.com+7haascnc.com+7machinesused.com+7
- Spindle bore/bar capacity: 2.31″ (≈44 mm) bore; supports bar feed up to ~1.75″ (44 mm) cncmachines.com+5haascnc.com+5machinestation.us+5
- Turret: 12-station bolt-on style for OD and ID tooling youtube.com+8haascnc.com+8exapro.com+8
- Rapid traverse: X/Z axis rapids up to ~1,200 ipm (30 m/min) machinestation.us+9haascnc.com+9machinesused.com+9
- Standard features: Chip auger, optional bar feeder interface, tool presetter, parts catcher, USB/RS232 connection cncmachines.com+8machinestation.us+8cncmachines.com+8
- Footprint & weight: Compact, floor space around 8 × 5 ft; weighs ~4,000–6,000 lb depending on configuration
HAAS DT‑1 Drill & Tap Machine

The HAAS DT‑1 Drill & Tap Machine is a compact, high-speed CNC machining center that streamlines drilling, tapping, and light milling in one efficient setup.
• Work Envelope: 20" × 16" × 15.5" (X/Y/Z) work cube with a 26" × 15" T‑slot table supporting up to 250 lb haascnc.com+13exportpagescdn.net+13technology-products.dksh.com.sg+13.
• Spindle: BT‑30 inline direct‑drive spindle—standard 10,000 RPM, optional up to 20,000 RPM; rigid tapping up to 5,000 RPM haascnc.com+4haas.co.uk+4exportpagescdn.net+4.
• Power: 15 hp vector drive delivering strong cutting torque (≈46 ft‑lb / 62 Nm) theequipmenthub.com+3ctemag.com+3haas.co.uk+3.
• Rapids & Acceleration: Fast 2,400 ipm (≈61 m/min) rapids with high acceleration (up to 1 g), and up to 1,200 ipm cutting feeds haascnc.com+6exportpagescdn.net+6haas.co.uk+6.
• Tool Handling: Side-mount 20 + 1 tool changer with ~1.8–1.6 s chip‑to‑chip time revelationmachinery.com+2exportpagescdn.net+2haas.co.uk+2.
• Chip & Coolant Management: Standard 45–55 gal flood coolant, steep-sloped enclosures, and optional twin chip augers haas.co.uk+4ctemag.com+4revelationmachinery.com+4.
• Footprint & Build: Lean-style, compact footprint made for dense production environments; built-in high-speed machining features revelationmachinery.com+6haas.co.uk+6ctemag.com+6.
• Additional Features: 15″ color LCD, USB/Ethernet, power-failure detection, anchor-ready cast‑iron base haas.co.uk+1exportpagescdn.net+1.
HAAS Mini-Mill
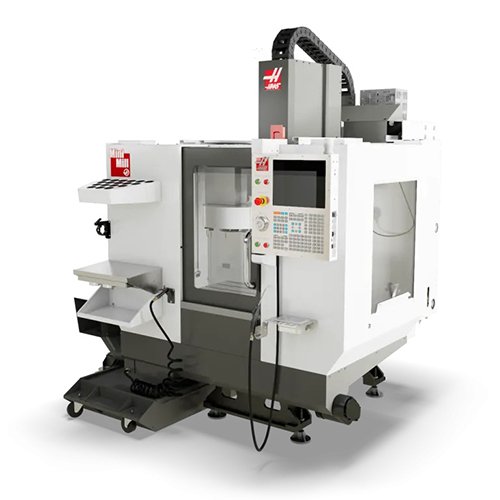
The Haas Mini Mill is a compact 3‑axis CNC vertical machining center that brings full-size milling capabilities in a small, efficient footprint—perfect for job shops, educational settings, or as a tight-space secondary spindle haascnc.com+14haascnc.com+14haas.co.uk+14.
• Work Envelope: X travel: 16″ (406 mm) | Y travel: 12″ (305 mm) | Z travel: 15″ (381 mm)
• Spindle: 40‑taper spindle, belt-driven | Base version: 8,000 rpm, 7.5 kW (10 hp) |Higher-end “Super Mini Mill” upgrade: 10,000 rpm & rigid tapping
• Table & Load: 36″ × 12″ table with 3 T‑slots | Max load 500 lb (227 kg)
• Feed Rates: Cutting feed up to ~650 ipm (16.5 m/min) | Rapid traverse up to ~800 ipm (20 m/min); Super variant ~¹²⁰⁰
• Tool Changer: Standard 10‑pocket carousel; optional 20‑pocket on Super Mini
HAAS VF2
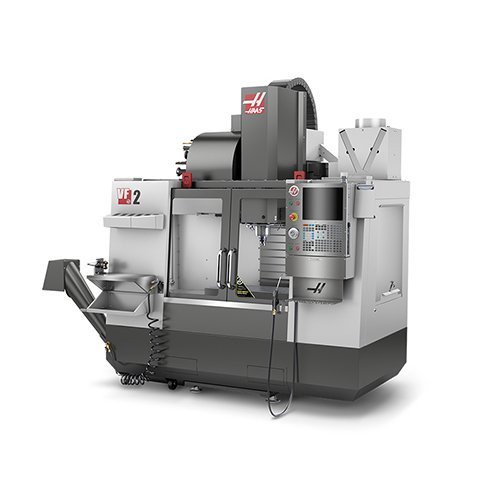
The Haas VF‑2 is the flagship small-frame 40‑taper vertical machining center in Haas’s VF Series—often described as the “workhorse” of the shop floor due to its versatility, performance, and robustness.
• Travel (X‑Y‑Z): 30″ × 16″ × 20″ (762 × 406 × 508 mm) work envelope
• Table: 36″ × 14″ with a 3,000 lb (1361 kg) load rating
• Spindle: 40‑taper, inline direct‑drive
◦ Standard: 30 hp vector drive, up to 8,100 rpm (90 ft‑lb torque)
◦ Optional gear‑box boosts torque to ~250 ft‑lb at 450 rpm
• Tool Changer: 20‑station carousel; fast ~4.2 s tool‑to‑tool, 4.5 s
• Rapid Traverse: 1,000 ipm (25.4 m/min) on X/Y/Z; cutting feed up to ~650 ipm
• Axis Thrust: X/Y: ~2,550 lb each; Z: ~4,200 lb
HAAS VF4
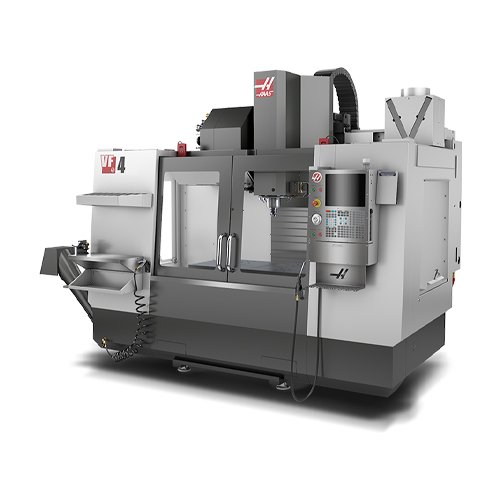
The Haas VF‑4 is a robust, mid‑size 40‑taper CNC vertical machining center—renowned as the step-up machine between the compact VF‑3 and the larger VF‑5—offering expansive travel and productivity in a dependable platform.
- Travel (X/Y/Z): 50″ × 20″ × 25″ (1,016 × 508 × 635 mm)
- Spindle: 40‑taper, direct‑drive, 30 hp vector drive with 8,100 rpm max (upgradable to 12,000 rpm on Super‑Speed models)
- Table Size & Load: 52″ × 19.5″ table with ~3,000–3,500 lb capacity
- Tool Changer: 20‑station carousel (side‑mount), ~4.2 s tool‑to‑tool & ~4.5 s chip‑to‑chip
- Rapids: 1,000 ipm on X, Y, Z (≈25 m/min) standard (~1,181 ipm in some units)
- Feeds: Up to ~650 ipm (≈16.5 m/min) cutting feed
Manual Department
Bridgeport Milling Machine
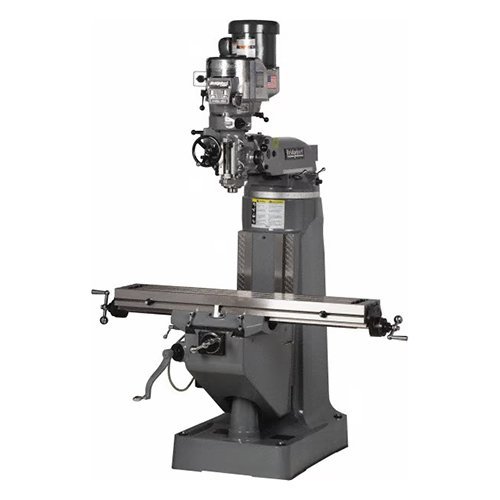
Bridgeport milling machine is a classic and widely recognized manual knee-type vertical milling machine known for its versatility, reliability, and precision. It features a movable quill and adjustable knee to handle a variety of milling, drilling, and boring operations.
Key Features:
- Variable-speed or step-pulley head with speeds typically ranging from 60–4,200 RPM
- Quill travel: ~5″ (127 mm); used for vertical drilling and boring
- Table travel: ~30″ × 12″ (X and Y) on standard models
- R8 spindle taper – supports a wide variety of tooling
- Manual or power feed options on axes
Hardinge Manual Lathe
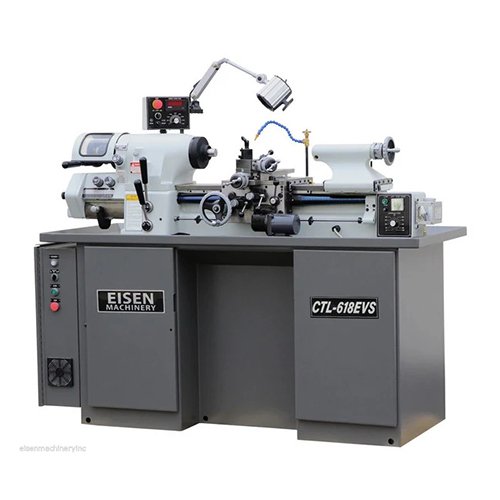
Hardinge manual lathe, particularly models like the HLV-H, is a renowned toolroom lathe known for its exceptional precision, smooth operation, and fine threading capabilities.
Key Features:
- Infinitely variable spindle speeds (typically up to ~3,000 RPM)
- 5C collet-ready spindle for precision work on small diameters
- Leadscrew and feed rod for independent threading and feeding
- Ultra-smooth cross-slide and carriage movement for micrometer-accurate control
- Known for exceptional surface finishes and tight tolerances
Inspection Department
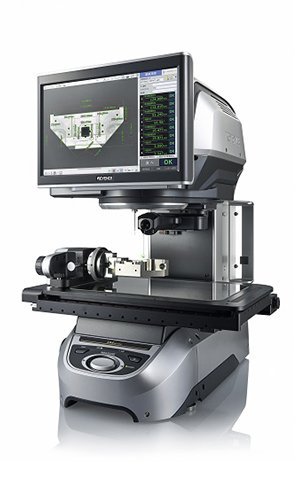
Keyence IM Series
Keyence IM Series is a high-speed, high-accuracy image dimension measurement system designed to instantly measure complex parts with minimal setup and operator input.
Key Features:
- Uses telecentric optics and high-resolution cameras for precise 2D measurements
- Capable of measuring up to 300 dimensions in seconds with just the push of a button
- Place-and-press operation—no need for part alignment or fixtures
- Built-in automatic edge detection and pass/fail judgment
- Repeatable, high-accuracy measurements (±2–4 µm depending on model)
- Hardness Testers – to confirm material properties and heat treatment
- Surface Finish Testers – for verifying critical finish specs
- Height Gages, Bore Gages, Micrometers, Calipers, Pin & Thread Gages, and more – all maintained and calibrated for precision