Our Quality Control for Military Parts govern the distribution of every fastener and electronic component from our facility. At TEC Aerospace, we have built our processes upon the rigorous requirements of the AS9120B standard, a quality management system specifically designed for aerospace distributors. This system is not a set of guidelines but a structured, auditable process that ensures the integrity, conformity, and reliability of the products we supply to the defense sector.
Quality Control for Military Parts: From Supplier to Shipment
Our approach to Quality Control for Military Parts begins with a stringent supplier qualification process, where we partner only with vetted suppliers on our Approved Supplier List and continuously monitor their performance. This secures the supply chain from its origin.
Upon arrival, every shipment undergoes a detailed incoming inspection. We verify physical parts against the purchase order and scrutinize all documentation, including the manufacturer's Certificate of Conformance (CofC). A part without a complete and authentic CofC is deemed non-conforming.
In our warehouse, we implement strict in-process controls to prevent damage and maintain full traceability, even when splitting lots into smaller quantities. We manage age-sensitive materials and prevent Foreign Object Damage (FOD). A final outbound inspection verifies order accuracy and documentation before shipping.
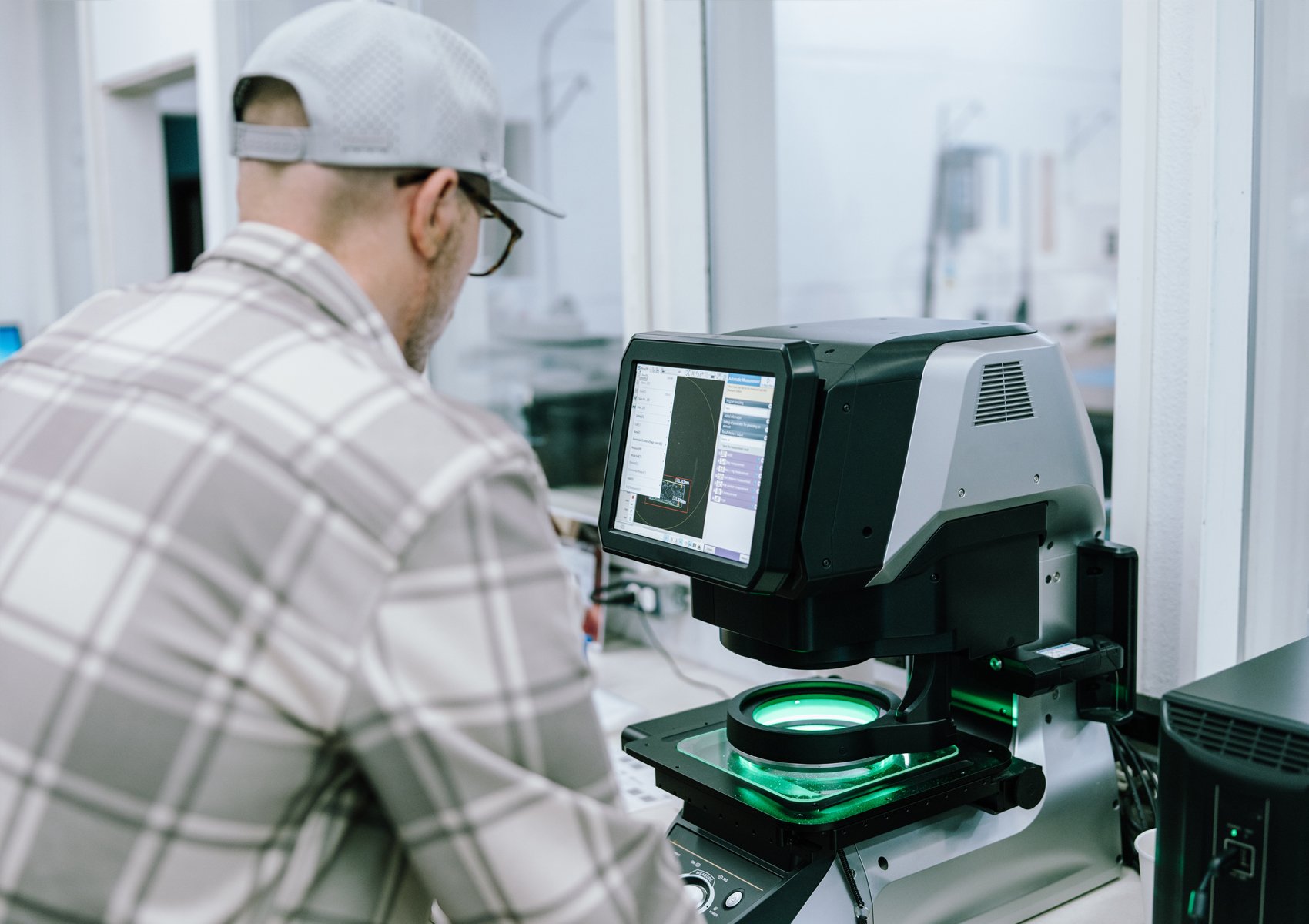
Manufacturing and Inspection Capabilities
Our Quality Control for Military Parts is supported by a robust combination of advanced CNC technology and traditional, high-precision manual machining.
- CNC Machining: Our fleet of Haas CNC machines, including ST-series lathes with live tooling, VF-series 5-axis mills, and high-speed Drill & Tap centers, forms the core of our production. This technology allows us to produce complex geometries from advanced materials like titanium and high-strength alloy steels, all while holding tolerances as tight as +/- 0.001 inches.
- Manual Department: For prototyping, one-off custom parts, or specialized secondary operations, our manual department provides essential versatility. Our skilled machinists utilize classic, high-precision equipment, including the Bridgeport manual milling machine for its reliability in milling, drilling, and boring, and the Hardinge manual lathe, renowned for its exceptional accuracy and ability to produce fine surface finishes. This department, along with our Marvel cut-off saws for material preparation, ensures we have the flexibility to meet any customer requirement.
- Inspection Department: Verification is the final word in our quality process. Our climate-controlled inspection department is equipped with state-of-the-art metrology tools to ensure every part meets its exact specifications. The centerpiece is our Keyence IM Series Image Dimension Measurement System, which uses telecentric optics to measure up to 300 dimensions on complex parts in seconds with incredible accuracy and repeatability. This is supplemented by a full suite of calibrated equipment, including Hardness Testers to confirm material properties, Surface Finish Testers, and a wide array of Height Gages, Bore Gages, Micrometers, Calipers, and Pin & Thread Gages.
Specialized Quality Control for Military Parts: Critical Components
For mission-critical military parts, we apply additional, specialized controls.
- Military-Grade Fasteners: We ensure absolute adherence to Military Specifications (Mil-Spec), procuring parts that conform exactly to standards such as MS, AN, and NAS. Our process includes verifying compliance with the Defense Federal Acquisition Regulation Supplement (DFARS) for specialty metals and confirming that every lot is traceable to a government-approved manufacturer. We review the manufacturer’s test reports to confirm that required mechanical property tests, such as for tensile and shear strength, have been performed and passed.
- Military-Grade Electronics: We address two primary risks: counterfeit parts and electrostatic discharge (ESD). To mitigate the threat of counterfeits, our first preference is to procure parts directly from Original Component Manufacturers (OCMs) or their authorized distributors. For components sourced elsewhere, we employ a risk-based inspection strategy that includes high-magnification visual inspection to look for signs of remarking or "blacktopping," X-ray analysis to examine internal construction, and, when necessary, destructive decapsulation to inspect the internal die markings. To protect against ESD, all sensitive electronics are handled exclusively within an ESD Protected Area (EPA). Inside the EPA, all personnel are grounded, typically with wrist straps, and all work surfaces are static-dissipative. Components are always stored and transported in specialized static-shielding packaging.
- Military Spare Parts: Our Quality Control for Military Parts extends to the entire range of military spare parts, which are essential for maintaining the operational readiness and life cycle of defense equipment. We adhere to a disciplined parts management program that prioritizes the selection of standard or commonly used parts to enhance reliability, maintainability, and interoperability. A critical component of our process is ensuring unimpeachable traceability for every spare part. We require and meticulously verify a complete documentation trail from the supplier back to the approved manufacturer, including Certificates of Conformance and, where applicable, chemical and physical test reports. This process is designed to confirm the part's authenticity and conformity to all government and military standards, mitigating risks and ensuring the integrity of the systems in which they are installed.
Quality Control for Military Parts: Non-Conforming Products and Accountability
Should a non-conforming military part be identified at any stage, it is immediately segregated into a secure quarantine area to prevent it from entering the supply stream. We then initiate a formal corrective action process to investigate the root cause of the issue and implement a permanent solution to prevent recurrence. This system of accountability ensures that every military part we deliver meets the high standards of safety and performance required by our military clients.